A área de Planejamento e Controle da Manutenção é responsável por boa parte do sucesso do setor de manutenção. Não querendo tirar o mérito das demais áreas, muito pelo contrário. O sucesso do setor de manutenção não depende de uma área exclusiva, mas de uma soma de esforços entre Planejamento e Controle da Manutenção, Manutenção Mecânica, Manutenção Elétrica, Instrumentação, Usinagem, Calderaria, e demais áreas. Porém, o Planejamento e Controle de Manutenção está presente em todos os processos de manutenção e colabora bastante para que tudo saia da melhor forma possível.
Desde a identificação de um problema até a sua correção e prevenção, a área de Planejamento e Controle da Manutenção estará presente para minimizar os riscos desse problema e levantar o maior número de informações possíveis para futuramente transformar essas informações em dados e traçar estratégias para elevar a disponibilidade e confiabilidade dos equipamentos.
Muitos profissionais desconhecem a importância do Planejamento e Controle da Manutenção e não conseguem enxergar o mar de oportunidades que essa área oferece, se bem gerenciada. Por esse motivo, resolvi listar aqui os 6 fatos sobre Planejamento e Controle da Manutenção que seu chefe quer que você saiba, para que você não entre para a lista dos profissionais que não conhecem a área estratégica da manutenção.
1. O Planejamento e Controle da Manutenção aumenta a produtividade dos serviços de manutenção em 30%
Boa parte do trabalho do Planejamento e Controle da Manutenção consiste em otimizar a utilização dos recursos. Encaramos como recurso tudo aquilo que investimos para que possamos desempenhar as atividades de manutenção, como: materiais, ferramentas, mão de obra e tempo.
De todos os recursos citados acima, o mais precioso deles é o tempo. O tempo é um recurso finito e uma vez perdido não será recuperado. Por essa razão, o Planejamento e Controle da Manutenção deve voltar boa parte da sua atenção para a otimização desse recurso tão valioso.
Sabe-se que em uma atividade realizada sem planejamento, existe 65% de desperdício de tempo. Ou seja, dentro das 8 horas normais de trabalho, apenas 2,8 horas são de fato aproveitadas. Esse número é assustador e a causa disso é explicada no infográfico abaixo:
Para minimizar ao máximo essa perda de tempo dentro das atividades de manutenção, o melhor a se fazer é implantar corretamente sistemáticas de Planejamento e Controle da Manutenção. Dessa forma, podemos dimensionar de forma assertiva o volume de atividades que devem ser feitas para manter os ativos disponíveis e confiáveis.
Após a implantação do PCM Planejamento e Controle da Manutenção, a expectativa é que o Tempo Produtivo de Trabalho suba de 35% para no mínimo 65%. Em um primeiro momento essa já é uma elevação gigantesca na produtividade da equipe, consiste basicamente em elevar o tempo produtivo de 2,8 horas para 5,2 horas.
2. Principais Padrões de Falhas dos Equipamentos
Ao contrário do que muitos profissionais pensam, as falhas têm padrões diferentes de nascimento e comportamento. É função do Planejamento e Controle da Manutenção identificar e catalogar os principais padrões de falhas que se apresentam nesses equipamentos.
Após o Planejamento e Controle da Manutenção ter conhecimento dos principais tipos de falhas que acometem os equipamentos, basta traçar as estratégias e aplicar determinadas técnicas de manutenção nos momentos certos.
Podemos dizer que as existem dois tipos de falhas basicamente: as falhas relacionadas a idade do equipamento e as falhas que não estão relacionadas com a idade do equipamento. Dentro desses dois tipos de falhas, encontramos os padrões de comportamento das falhas.
John Moubray, grande pesquisador e um dos principais teóricos da Manutenção Centrada na Confiabilidade, realizou um estudo estatístico, dentro da Indústria Aeronáutica, e atestou a existência de diferentes tipos de Curvas, ilustradss a seguir:
Curva da Banheira
A curva da banheira é amplamente utilizada na engenharia de confiabilidade. Ela descreve uma forma particular a performance do equipamento, sendo basicamente divida em três fases:
- A primeira parte é uma taxa de falha decrescente, conhecida como falhas iniciais.
- A segunda parte é uma taxa de falha constante, conhecida como falhas aleatórias.
- A terceira parte é uma taxa de falha crescente, conhecida como falhas de desgaste.
A curva tem esse nome por se assemelhar a uma banheira: lados íngremes e um fundo plano.
A curva da banheira é gerada pelo mapeamento da taxa de falhas precoce de “mortalidade infantil” quando introduzidas pela primeira vez, a taxa de falhas aleatórias com taxa de falha constante durante sua “vida útil” e, finalmente, a taxa de falhas de “desgaste” à medida que o produto excede sua vida de design.
Envelhecimento Lento
Esse padrão está relacionado diretamente a idade do equipamento e na medida em que o equipamento envelhece, as falhas aumentam. Esse padrão é característico em sistemas hidráulicos e equipamentos mecânicos, que com o passar dos anos, a fadiga dos materiais e o desgaste são as principais causas da falha.
Visão Tradicional do Envelhecimento
Desenvolvimento Rápido seguido de Aleatoriedade
Esse padrão se caracteriza pelo fato de ter um índice crescente de falhas no início de sua vida útil e com o passar do tempo, por consequência de ações de manutenção, entra em um nível estável de aleatoriedade das falhas.
Em média, 7% desses equipamentos apresentam esse padrão. Esse padrão não está ligado ao envelhecimento do equipamento.
Falhas Aleatórias
Representam uma fatia de 14% entre os padrões. Geralmente são característicos em equipamentos elétricos e eletrônicos.
Mortalidade Infantil
É importante reconhecer esse parão. A Mortalidade Infantil representa, em média, sessenta e oito por cento dos equipamentos e possuem uma probabilidade condicional de falha imediatamente após a instalação e o comissionamento.
A maioria das falhas de itens foram induzidas por atividades diretamente relacionadas a substituições e revisões baseadas em tempo. Esse tipo de padrão é aleatório e encontrado principalmente em softwares e sistemas informatizados.
Panorama Geral dos Padrões de Falha
Um fato interessante sobre essas curvas é o baixo índice de itens que exibem uma região de desgaste distinta, o grande número de itens que exibem uma região de falha aleatória e o alto índice de itens que se apresentam na região de mortalidade infantil.
Somente três os padrões (Mortalidade Infantil, Curva da Banheira e Envelhecimento Lento) representam apenas onze por cento dos itens estudados exibem a região de desgaste indicada por uma probabilidade condicional de aumento rápido na extremidade direita da curva e estão relacionados a idade do equiapemento.
Oitenta e Nove por cento dos equipamentos tem pelo menos alguma região de falhas aleatórias denotadas por uma região plana na curva e não tem ligação com a idade do equiapemento.
Isso significa que 89% dos equipamentos podem se beneficiar de algum tipo de monitoramento de condição e que apenas 11% podem se beneficiar de reposição ou revisão com base no tempo.
3. O que é Curva PF
Os equipamentos não trabalham sempre sem problemas técnicos. Quando as falhas surgem de forma inesperada, a produção para, a manutenção é chamada com urgência, a equipe técnica tem de detectar a origem da falha, identificar e substituir as peças danificadas e definir o melhor processo para recolocar o equipamento em pleno funcionamento. Quando estas situações surgem a sua reparação pode demorar desde alguns minutos, até dias, o que implica custos elevados e altos índices de stress nas equipes de manutenção.
É função do Planejamento e Controle da Manutenção identificar a Curva PF de cada equipamento e usa-la como uma ferramenta analítica para ações proativas de manutenção.
- Uma falha é uma condição insatisfatória. Por outras palavras, uma falha é um desvio identificável da condição original que é insatisfatória para um determinado usuário.
- Uma falha potencial é uma condição física identificável que indica que uma falha funcional é iminente e geralmente é identificada por um Técnico de Manutenção usando manutenção preventiva preditiva ou quantitativa.
- Uma falha funcional é a incapacidade de um item (ou o equipamento que o contém) atender a um padrão de desempenho especificado e geralmente é identificado por um operador.
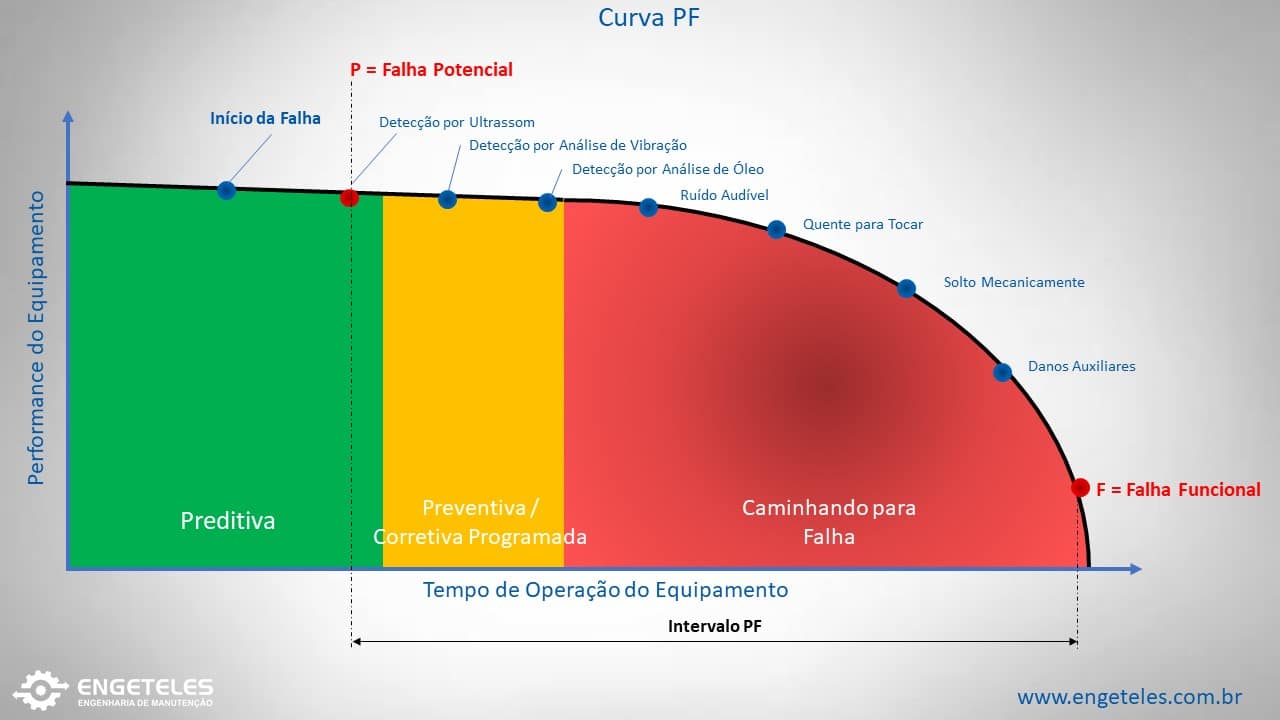
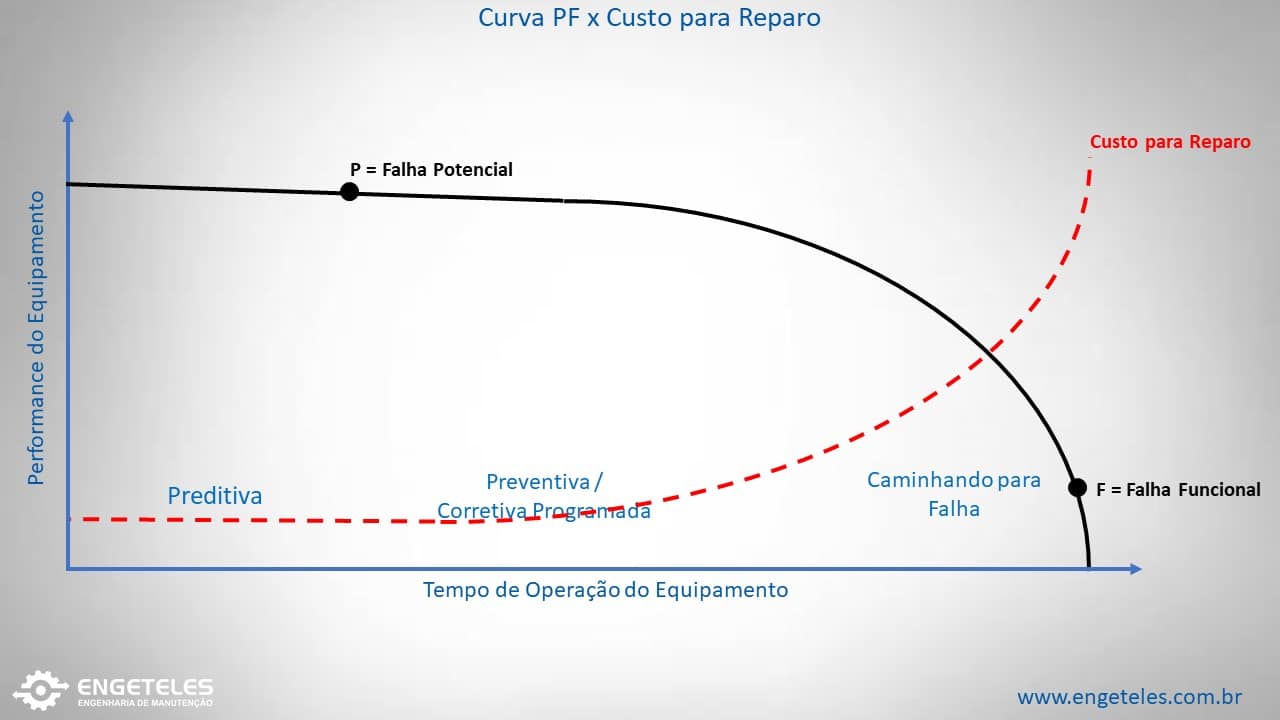
4. Árvore de Custos da Manutenção
Como visto no item acima, o custo de manutenção se eleva quando o equipamento foi acometido ou está próximo de uma falha funcional. Isso tem uma explicação bem simples: quando um equipamento interrompe um processo de produção ou causa a sua perda de performance, ocorre o que chamamos de lucro cessante.
Lucros cessantes são prejuízos causados pela interrupção de qualquer das atividades de uma empresa, no qual o objeto de suas atividades é o lucro. Exemplos de lucros cessantes são: não vender um produto por falta no estoque; uma máquina que para e deixa de produzir; um acidente de trânsito que tira ônibus ou táxis de circulação; um advogado que tem seu voo trocado e perde a hora de uma audiência, etc.
Uma função vital do Planejamento e Controle da Manutenção é elaborar uma árvore de custos e identificar quais são as maiores fontes consumidoras dos investimentos destinados para manutenção dos equipamentos. Geralmente dentro da árvore de custos, a maior fatia sempre será referente aos custos indiretos, mais especificamente o lucro cessante.
Por esse motivo se faz necessário ter bons planos de manutenção. Se o Planejamento e Controle da Manutenção elabora e gerencia da forma correta os planos de manutenção, os índices de falhas dos equipamentos caem e por consequência, a parada dos equipamentos diminui absurdamente. Essa reação em cadeia impactará diretamente de forma positiva nos custos de manutenção.
Custos Diretos de Manutenção
Os custos diretos de manutenção são compostos por:
- Peças de Reposição
- Ferramentas
- Mão de Obra
- Insumos
Custos Indiretos de Manutenção
- Lucro Cessante
- Depreciação
- Custos Induzidos (Multas, Juros, Etc.)
Veja abaixo o cenário mais comum para uma árvore de custos de manutenção:
5. Retorno Financeiro do OEE
Você sabe o que é OEE? OEE – Overall Equipment Effectiveness, que em tradução livre significa, Eficiência Global do Equipamento, é um dos indicadores mais usados por industrias de grande porte no mundo todo. Este índice é capaz de medir e representar a verdadeira realidade da eficiência operacional no chão de fábrica.
Desenvolvido e introduzido por Seiichi Nakajima, um dos desenvolvedores da metodologia TPM (Total Productive Maintenance), como uma medida fundamental para se avaliar a performance de um equipamento, sendo usado como um dos componentes fundamentais da do TPM.
Cada dia que se passa cresce a busca pela maior produtividade e o menor custo, dessa forma, várias ferramentas e metodologias são cada vez mais utilizadas no ambiente fabril com o objetivo de alcançar o números impostos. Uma dessas metodologias é a Lean Manufacturing, que prega a filosofia da manufatura enxuta e foi onde o OEE começou a ser disseminado.
Ao contrário do que muitos profissionais pensam, o OEE está diretamente ligado ao trabalho do Planejamento e Controle da Manutenção.
O OEE é o produto de três linhas básicas de uma industria, que são: qualidade, disponibilidade e performance.
A fórmula para calcular OEE é:
OEE = DISPONIBILIDADE X QUALIDADE X PERFORMANCE
O retorno financeiro do OEE é incrível! E para elevar o OEE é simples, basta elevar o índice de disponibilidade, qualidade ou performance. Todos os três itens estão ligados ao trabalho do Planejamento e Controle de Manutenção.
Estudos comprovam que a elevação de 1% do OEE reflete em 3% a 7% na elevação do lucro líquido da organização. Ou seja, se o Planejamento e Controle de Manutenção conseguir emplacar uma estratégia que garantirá a elevação desse indicador, certamente a empresa lucrará mais.
Há exemplos comprovados de que uma melhora de 10% no OEE leva a indústria a ter uma elevação em seu resultado de 30% ou mais. Isso nos mostra a importância de conhecer e controlar esses indicadores.
6. Fator de Produtividade da Mão de Obra
Uma falha muito comum no Planejamento e Controle da Manutenção é não usar o fator de produtividade da mão de obra durante a etapa do planejamento das atividades da manutenção.
O Fator de Produtividade da Mão de Obra, também chamado de Wrench Time (“Tempo na Ferramenta” em inglês) é o tempo em que o colaborador passa produzindo alguma atividade que gera valor agregado para a empresa.
Esse tempo não inclui a obtenção de peças, ferramentas, instruções ou deslocamento necessário para a realização das tarefas. Não inclui o tempo gasto na obtenção de instruções para realização do trabalho. Obviamente, não inclui tempo de intervalo para refeições, idas ao banheiro, paradas para o “cafezinho”, dentre outros intervalos. Ou seja, essas tarefas em que o profissional passa sem estar de fato com a mão na massa são muitas vezes necessárias para fazer o trabalho, mas não são “tempos produtivos”.
Um erro muito comum é achar que o colaborador está disponível 8 horas da sua jornada de trabalho para realizar as atividades de manutenção.
Temos que descontar todo o tempo que ele leva para realizar as atividades improdutivas e encontrar o fator de produtividade daquela mão de obra, antes de realizar o planejamento e programação daquelas atividades.
Para exemplificar, vamos imaginar a seguinte situação:
João é um mecânico industrial que trabalha no turno administrativo em uma indústria cimenteira, com início da sua jornada às 08:00 e fim às 17:480, de segunda à sexta. Logo, são 8,48 horas diárias e 44 horas semanais.
A rotina de João é basicamente a mesma todos os dias. No exemplo abaixo ele irá trocar os rolamentos de uma bomba hidráulica:
08:00 | 08:15 | Diálogo Diário de Segurança |
08:16 | 09:00 | Reunião de Passagem de Serviços |
09:01 | 09:08 | Descolamento até o almoxarifado |
09:09 | 09:40 | Obtenção de Peças e Ferramentas no Almoxarifado |
09:41 | 09:51 | Deslocamento até o local que será realizado a manutenção |
09:52 | 10:05 | Preenchimento da APR |
10:06 | 10:20 | Aguardando Liberação do Técnico de Segurança para início do trabalho |
10:21 | 11:45 | Execução da Atividade de Manutenção – Desacoplar conjunto motor e bomba |
11:46 | 12:00 | Parada para Almoço (tempo para lavar mãos, guardar ferramentas e deslocamento até o refeitório) |
12:01 | 13:00 | Intervalo para Almoço |
13:01 | 13:10 | Retorno do Almoço (deslocamento até a máquina) |
13:11 | 14:30 | Execução da Manutenção – Desmontagem da bomba |
14:31 | 14:50 | Deslocamento até a oficia de usinagem (João identificou a necessidade de tornear o eixo da bomba para acertar as medidas de tolerância para montagem dos novos rolamentos) |
14:51 | 15:30 | Aguardando que o torneiro realize o serviço |
15:31 | 15:41 | Deslocamento até o local da manutenção |
15:42 | 16:45 | Execução da Manutenção – Montagem da Bomba, Testes e Organização do Local de Trabalho |
16:46 | 17:00 | Aguardando o Eletricista rearmar o motor elétrico |
17:01 | 17:10 | Preenchimento da Ordem de Serviço |
17:11 | 17:20 | Aguardando Supervisores da Produção e Manutenção validarem o serviço |
17:20 | 17:48 | Limpeza Pessoal e preparação para o fim da jornada |
As linhas em amarelo destacam os momentos em que João estava sendo realmente produtivo e atuando diretamente na máquina. Podemos ver que ele atuou diretamente na máquina apenas 3,46 horas e isso representa apenas 40% das 8,48 horas diárias de sua jornada de trabalho. Ou seja, o fator de produtividade de João é 40%.
O que isso significa?
Que ao planejar e programar uma atividade de manutenção, o PCM deve considerar apenas 3,46 diárias de trabalho, tendo em vista que as demais horas são improdutivas. Sendo essa improdutividade necessária ou não.
IMPORTANTE: Para medir o fator de produtividade, nunca devemos nos basear em um único dia de trabalho e em um único colaborador. Devemos medir por no mínimo 7 dias, em atividades diferentes e em colaboradores diferentes. Levando em consideração condições climáticas, localização dos equipamentos e características pessoais dos colaboradores.
Benchmarking do Fator de Produtividade
A grande maioria das industrias têm um fator de produtividade parecido, girando em 30% e 40%. Esse fator pode variar dependendo de alguns fatores:
- Segmento da Indústria/Empresa
- Especialidade da Mão de Obra (Mecânica, Elétrica, Instrumentação, etc.)
- Localização Geográfica dos Equipamentos
- Quantidade de Mão de Obra Disponível
- Autonomia (ou a falta dela) dos funcionários
Fator de Produtividade de Classe Mundial
Um valor aceitável e completamente atingível para o fator de produtividade em níveis globais variam entre 60% e 70%.
Alguns ajustes nos processos e procedimentos de manutenção, treinamentos com as equipes e introdução de novas metodologias e ferramentas podem fazer com que esse índice suba facilmente. planejamento e controle da manutenção