Você conhece a metodologia TPM – Total Productive Maintenance?
Total Productive Maintenance no nosso bom português significa Manutenção Produtiva Total.
Como o próprio nome já diz, o TPM é uma metodologia que visa transformar a manutenção em uma fonte de resultados lucrativos para a empresa, elevando sua performance, otimizando e aproveitando ao máximo seus recursos, redesenhando os processos de operação e manutenção, através do desenvolvimento de todo o pessoal envolvido.
A ideia é basicamente ter uma produção perfeita, garantida pela manutenção dos equipamentos realizada melhor forma possível, onde os objetivos principais são:
- Eliminar qualquer parada indesejada (seja provocada por uma falha de manutenção ou falha operacional);
- Não diminuir o ritmo operacional e manter a produção sempre no ritmo mais alto possível;
- Qualidade 100%! Não produzir nenhum produto com defeito, tudo dever ser perfeito;
- Zero acidentes de trabalho.
O TPM combina as manutenções pró-ativas, preditivas e preventivas de uma forma que maximiza a performance e eficiência operacional dos equipamentos. Ele mescla as habilidades do pessoal de manutenção e produção, colocando uma forte ênfase no desenvolvimento técnico dos operadores para que eles possam ajudar a manter seus equipamentos.
Implantar a metodologia TPM em uma fábrica é um processo que requer tempo, disciplina e bastante capacitação das pessoas envolvidas. A capacitação e multiplicação das informações com certeza são os pontos mais importantes e que definirão o sucesso do programa. O trabalho em equipe também é fundamental, cria-se um nível de responsabilidade dos operadores e mantenedores sobre o equipamento, onde cada funcionário “adotará” um equipamento e tudo que acontecer de anormal com aquele equipamento será de responsabilidade daquele funcionário.
Após a metodologia implantada, os resultados são incríveis! A melhoria na produtividade é a primeira mudança que será notada, o entrosamento das equipes se destaca e os indicadores começam a decolar! Parece sonho, não é?!
Para te mostrar que isso é totalmente possível, iremos fazer uma série de posts mostrando como funciona a implantação do TPM. Esse é o primeiro post, onde iremos fazer um overview da metodologia e explicar como ela surgiu.
Conhecendo a história do TPM
O TPM foi desenvolvido no Japão na década de 1960, poucos anos após a 2ª Guerra Mundial ter devastado o país. As indústrias precisavam se reerguer rapidamente para reaquecer a economia e esse crescimento deveria ser totalmente sustentável, a prova de erros e acontecer de forma sincronizada.
Na década de 1950, as teorias americanas foram adotadas pelos japoneses e adaptadas à gestão de suas fábricas. Na década seguinte, é criado o prêmio da excelência em manutenção produtiva (PM) pela Associação Japonesa de Manutenção e é fundado o JIPES (Japan Institute of Plant Engineers, “Instituto Japonês de Engenheiros de Fábrica”), que se tornaria o JIPM (Japan Institute of Plant Maintenance, “Instituto Japonês de Manutenção de Fábrica”). A sigla TPM foi registrada pelo JIPM.
O TPM também é bastante conhecido pelos seus pilares, que dinamizam a sua implantação e edificam de forma sólida a metodologia.
Pilares do TPM
Os pilares do TPM são divididos em 8 atividades de apoio e uma fundação que é a metodologia 5s. Essas atividades de apoio são chamadas de pilares pelo fato de todas terem a mesma importância e peso no sucesso da metodologia, e qualquer um desses pilares que não for bem desenvolvido e implantado comprometerá todo o trabalho.
Cada pilar tem uma sequencia de etapas para sua implantação, esse sequencia tem em média de 5 a 7 etapas, que formam um passo a passo para uma implantação bem sucedida.
BASE – 5S
O primeiro passo para buscar a implantação da metodologia TPM é implantar a metodologia 5s. O 5s é a base que dará sustentação ao programa e irá preparar a fábrica para toda a mudança que será provocada pelo TPM.
O TPM traz um impacto muito grande na rotina de trabalho dos colaboradores e envolve um grande processo de mudança cultural. Se tentarmos implantar um programa complexo como o TPM em uma fábrica que não tem nenhum tipo de controle ou metodologia de gestão, pode ter certeza que a implantação não terá sucesso e o programa será abandonado.
O 5s irá organizar a casa e moldar a mente dos colaboradores, preparando-os para a mudança. Cria um ambiente de trabalho limpo e bem organizado, ferramentas e peças ficarão muito mais fáceis de encontrar, e é muito mais fácil de detectar questões emergentes, como vazamentos de fluido, derramamentos de materiais, aparas de metal de desgaste inesperado, fissuras em mecanismos, etc.
A metodologia 5S se baseia em 5 sensos, que devem ser implantados de forma ordenada:
- Seiri – Utilização (eliminar qualquer coisa que não é realmente necessário na área de trabalho);
- Seiton – Ordenação (organizar os itens restantes);
- Seisou – Limpeza (limpo e inspecionar a área de trabalho);
- Seiketsu – Saúde (criar padrões para realizar as atividades de forma segura e saudável);
- Shitsuke – Disciplina (garantir os padrões são regularmente aplicados).
PILAR 1 – MANUTENÇÃO AUTÔNOMA
O pilar de manutenção autônoma visa dar mais autonomia para os operadores, transformando-os em operadores técnicos. Essa autonomia consiste em pequenas atividades de manutenção de rotina, tais como limpeza, lubrificação, inspeções, ajustes, reapertos, etc.
O momento de implantação desse pilar é bem criterioso e todos os tramites devem ser conduzidos com muita atenção. Dar autonomia a um operador para que ele realize serviços de manutenção, por menores que sejam, requer algumas ações preparatórias.
O operador passará a executar novas atividades e isso requer um alinhamento prévio entre o colaborador, sua gerência e a empresa. O operador deve receber treinamentos sobre suas novas atribuições, ferramentas e condições de trabalho para executa-las com segurança.
Nessa fase, o operador passará a ser o dono do equipamento. E todas as ações rotineiras de manutenção serão de responsabilidade do operador, cabendo aos técnicos de manutenção apenas os trabalhos mais criteriosos, técnicos e que necessitam de uma maior expertise, mas ainda assim, o operador deve acompanhar a atuação do técnico de manutenção.
Os gestores também são peças fundamentais nesse processo. Com certeza, em um primeiro momento alguns operadores irão ter objeções contra as novas atribuições e é papel do gestor explicar a importância da implantação desse pilar e servir como um facilitador de todo o processo.
Como a Manutenção Autônoma ajuda?
- Dá aos operadores uma maior “propriedade” dos seus equipamentos;
- Aumenta o conhecimento dos seus dos operadores;
- Garante equipamento está limpo, ajustado e lubrificado;
- Identifica questões emergentes antes que se tornem falhas;
- Liberta o pessoal de manutenção para as tarefas de nível mais avançado superior.
PILAR 2 – MANUTENÇÃO PLANEJADA
O pilar de Manutenção Planejada consiste na criação e execução dos planos de manutenção, que abordam todas as atividades programadas com base no tempo, que devem ser realizadas em caráter preventivo e que tem como objetivo prever e reduzir as falhas a zero.
Esse pilar é voltado para as equipes de manutenção, que tem como objetivo principal elevar os índices de confiabilidade e disponibilidade dos equipamentos, reduzir custos com paradas indesejadas e desperdícios oriundos da falta de planejamento de atividades.
Quando o pilar de Manutenção Autônoma já está implantado, fica muito mais fácil implantar o pilar de Manutenção Planejada, pelos motivos abaixo:
- A equipe de manutenção terá mais tempo para dedicar à Manutenção Planejada, uma vez que as atividades mais simples e de rotina serão de responsabilidade do pessoal de operação;
- As máquinas estarão limpas, lubrificadas e ajustadas e isso facilitará as manutenções preventivas de maior porte;
- Identificação de falhas recorrentes e que merecem atenção.
Esse pilar deve mapear todo o processo de manutenção e com base nas informações colhidas, criar os planos de manutenção de forma que otimize os recursos da manutenção. Esse mapeamento deve começar pelos equipamentos, definindo quais são os mais importantes no processo de produção e merecem maior atenção. Também é necessário mapear as peças e materiais sobressalentes que serão necessários para manter o cronograma de manutenção por um determinado período de tempo. Outro ponto importante é o desenvolvimento da matriz de habilidades dos técnicos de manutenção, essa ferramenta é extremamente importante para definir quais profissionais estão aptos para cada atividades e quais pontos são necessários desenvolver em cada um deles, para que dessa forma a equipe fique cada vez mais completa e multidisciplinar.
Quais são os benefícios da Manutenção Planejada?
A partir do momento que se implanta as ações planejadas de manutenção, é natural identificar falhas em seu estágio inicial e agir com rapidez, evitando que essa falha potencial se transforme em uma falha funcional, ou seja, pare o processo de produção.
É comum a elevação de indicadores como MTBF, Disponibilidade e Confiabilidade, e como consequência vem junto a redução de custos. Além disso, as melhoria nos quesitos de qualidade do produto e segurança do trabalho também são perceptíveis.
PILAR 3 – MELHORIAS ESPECÍFICAS
A melhoria específica inclui todas as atividades que maximizam a eficácia global dos equipamentos, processos e plantas através de uma intolerante eliminação de perdas e da melhoria de rendimentos.
Muitas pessoas perguntam qual é a diferença entre a melhoria específica e as atividades de melhoria contínua diária que já praticam. O ponto básico a lembrar sobre a melhoria específica é que se uma empresa já está fazendo todas as melhorias possíveis durante o trabalho rotineiro e as atividades de pequenos grupos, a melhoria específica é desnecessária. Porém, as melhorias do dia-a-dia, na prática não marcham tão regularmente como seria desejável. As pessoas se queixam de estarem muito ocupadas, que as melhorias são difíceis de fazer, ou que não se atribui investimentos suficientes. Como resultado, os problemas difíceis permanecem sem solução e continuam as perdas e o desperdício, fazendo ainda mais remota a possibilidade de melhorar.
Todo processo é passível de melhoria e essas necessidades de melhorias podem ser identificadas durante a implantação da manutenção autônoma e manutenção planejada. As melhorias podem ter os mais variados objetivos, por exemplo: redução no tempo de produção, redução de custos operacionais, diminuição de tempos de setups, aumento dos níveis de segurança, etc.
A partir do momento que é identificada a necessidade de melhoria, devem ser definido o grupo de melhoria. Esse grupo deve ser composto por pessoas que atuam diariamente naquele processo e pessoas que tenham conhecimento técnico para atuar no projeto, como executores, auditores ou multiplicadores.
PILAR 4 – EDUCAÇÃO E TREINAMENTO
Não existe melhoria de processos sem o desenvolvimento de pessoas. Todo o trabalho deve consistir em desenvolver as pessoas para que em seguida, elas melhorem os processos.
Com a grande quantidade de novas atribuições para todos os funcionários do chão de fábrica (produção e manutenção), é necessário construir uma matriz de treinamentos para toda a equipe.
Os profissionais de Recursos Humanos são os responsáveis para apoiar diretamente esta fase (embora já tenham sido envolvidos desde o início), pois serão responsáveis diretos para revisar a descrição de cargos dos operadores, incluindo as novas atribuições que terão na prática do TPM.
Com o desenvolvimento da tecnologia de equipamentos e instrumentos de controle o trabalho dos operadores está numa transição de manual para monitoramento e supervisão. Através de treinamento no local de trabalho e Manutenção Autônoma os operadores adquirem habilidades relacionadas ao tratamento do equipamento.
Deve-se construir uma matriz de habilidades, que permitirá a visualização do nível de habilidade de cada colaborador, em cada função.
Uma boa prática também é a criação de uma oficina escola dentro da empresa. Esse ambiente terá todos os recursos necessários, como bancada de testes, apostilas, instrumentos e simuladores capazes de representar as máquinas em campo e permitir o treinamento de funcionários de forma prática, segura e didática.
PILAR 5 – SEGURANÇA E MEIO-AMBIENTE
O principal objetivo desse pilar é acidente zero, além de proporcionar um sistema que garanta a preservação da saúde e bem estar dos funcionários e do meio ambiente.
A observação das leis trabalhistas, bem como o respeito às normas de gestão e legislação ambiental, são pontos relevantes e que devem ser considerados para melhorar os índices de qualidade referentes a estes setores da empresa em fase de implantação da política TPM.
Pontos que devem ser considerados são:
- Inspeções voltadas para segurança operacional dos equipamentos;
- Desenvolvimento de processos de manutenção que elevam a segurança das atividades;
- Melhorias nos ambientes de trabalho visando adequações na ergonomia dos colaboradores, eliminação dos riscos de acidentes, melhoria na iluminação e sinalização, etc.
- Adequação de funcionários, instalações e equipamentos às Normas Regulamentadores (Ex: NR-10, NR-12, NR-33, NR-35, etc.)
- Desenvolvimento de sistemas de coleta seletiva de resíduos provenientes das manutenções.
PILAR 6 – MANUTENÇÃO DA QUALIDADE
A Manutenção da Qualidade consiste na definição e padronização das condições dos equipamentos, de forma que eles não produzam produtos defeituosos. Mas como isso é possível?
Estes defeitos são prevenidos através de verificação e medição periódicas das condições dos equipamentos. Desta forma, os defeitos potenciais são previstos pela análise de tendências de valores relacionados aos limites específicos e posteriormente tomadas de ação. Ou seja, fazer que as condições de operação sejam “á prova de erro”, esse conceito vem da técnica japonesa Poka-Yoke.
Poka-yoke (pronuncia-se poca-ioquê) é um dispositivo a prova de erros destinado a evitar a ocorrência de defeitos em processos de fabricação e/ou na utilização de produtos. Este conceito faz parte do Sistema Toyota de Produção e foi desenvolvido primeiramente por Shigeo Shingo, a partir do princípio do “não-custo”.
Um exemplo é a impossibilidade de remover a chave da ignição de um automóvel se a sua transmissão automática não estiver em “ponto morto”, assim o motorista não pode cometer o erro de sair do carro em condições inseguras. No Brasil as primeiras fábricas a utilizarem algum método poka-yoke foram as montadoras de veículos, como Volkswagen e Ford que notaram a prática utilizada por montadoras japonesas após o estudo de James Womack, divulgado no livro A Máquina que mudou o Mundo e culminou com o surgimento do Lean Enterprise Institute, dos EUA e logo em seguida do Lean Institute Brasil, institutos especializados na disseminação do Toyota Production System e Lean Manufacturing em empresas de todos os setores.
As origens dos defeitos podem ser classificadas em:
Materiais – A correta especificação de materiais e o desenvolvimento de fornecedores qualificados trazem como conseqüência a tendência de produtos sem defeitos.
Equipamentos – Pesquisar equipamentos que não produzem defeitos e melhorar os que produzem é outra forma de atingir produtos livres de defeitos.
Métodos – Encontrar métodos que não criam defeitos além de melhorar aqueles que criam é fundamental para a obtenção do zero defeito.
Pessoas – Desenvolver operadores competentes através da manutenção autônoma e treinamento em habilidades tem como conseqüência óbvia a detecção de anormalidades, a correção e restauração e a manutenção e controle da qualidade.
PILAR 7 – CONTROLE INICIAL
Como o nome já diz, o controle inicial aplica-se a equipamentos e processos novos, que serão adquiridos a partir de uma necessidade identificada durante ou após a implantação da metodologia TPM.
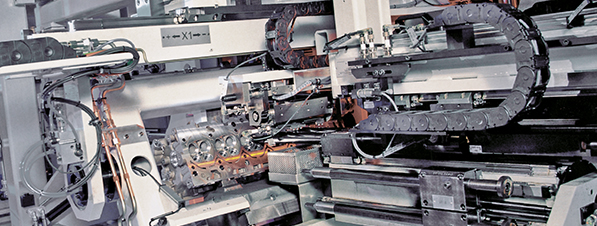
Os principais benefícios são:
- Novos equipamentos atingem níveis de desempenho planejados muito mais rápido devido ao menor número de problemas de inicialização.
- A manutenção é mais simples e devido à avaliação prática e envolvimento dos trabalhadores antes da instalação.
PILAR 8 – GESTÃO ADMINISTRATIVA
Esse pilar se define como uma extensão dos trabalhos aplicados no chão de fábrica para os ambientes administrativos.
Funções que são consideradas de “bastidores” também passam por transformações em seus processos, deixando-os mais claros, seguros e ágeis.
Os principais setores que passam por modificações são:
- PCM – Planejamento e Controle de Manutenção;
- PCP – Planejamento e Controle de Produção;
- Suprimentos;
- Almoxarifado;
- Segurança do Trabalho;
- Qualidade;
- Meio-Ambiente.
Esses setores estão diretamente ligados ao chão de fábrica e as ações da manutenção também impactarão de forma direta ou indireta eu seus resultados. Por isso, o motivo de estender os trabalhos até esses setores.
Esse foi o primeiro post da nossa série sobre TPM – Total Productive Maintenance. O tema do próximo artigo é: Implantação do Pilar Manutenção Autônoma – Passo a Passo.
Se você quer ser avisado quando esse artigo estiver no ar, deixe seu e-mail abaixo!