A Engenharia de Manutenção é um pilar indispensável dentro de uma empresa que busca transformar o setor de manutenção em uma fonte de resultados. Muito se fala sobre Engenharia de Manutenção, mas afinal, o que é a Engenharia de Manutenção?
A Engenharia de Manutenção projeta modificações e melhorias em equipamentos, processos e sistemas, com o objetivo de otimizar três itens: confiabilidade, disponibilidade e mantenabilidade.
A base do trabalho da Engenharia de Manutenção está na Análise RAM – Reliability, Avaliability e Maintenability. Em português, Confiabilidade, Disponibilidade e Mantenabilidade.
Confiabilidade é a probabilidade de um determinado item, equipamento, sistema ou processo, desempenhar a sua função requeridade em um determinado período de tempo. (Por exemplo, uma bomba centrífuga tem 95% de probabilidade de continuar operando nas próximas 8000 horas) .
A Disponibilidade é a porcentagem de tempo em que um equipamento esteve desempenhando a sua função requerida. (Por exemplo, no último mês a bomba centrífuga BOMB-0001 teve uma disponibilidade de 98%)
A Mantenabilidade (ou manutenabilidade) é a facilidade de se executar a manutenção. Também pode ser definida como a probabilidade de um técnico executar a manutenção de acordo com o prazo determinado.
A função do Engenheiro de Manutenção é conduzir projetos em que se eleve alguns dos três pilares. Dessa forma, é possível ter um processo de produção mais seguro, confiável e produtivo.
Alguns números que demonstram a importância de se trabalhar com Engenharia de Manutenção:
- Em média, uma indústria química de grande porte pode ter um prejuízo médio de R$100 mil/por hora, devido ao lucro cessante causado por quebra de equipamentos;
- Nas refinarias de petróleo, as perdas de produção representam cerca de R$12 milhões por ano para cada 1% de indisponibilidade;
- Nas refinarias de petróleo, a equipe de manutenção representa cerca de 30% da mão de obra total;
- Os custos com manutenção representam a maior parte dos custos operacionais, após os custos com energia elétrica e matéria prima;
- Todos os anos, mais de US $ 300 bilhões são gastos em manutenção e operação de usinas nos EUA, e estima-se que cerca de 80% destes gastos são destinados para manutenções corretivas emergenciais.
Engenharia de Manutenção e a Análise RAM
A RAM tem um impacto direto no lucro por meio da perda de custos de produção e manutenção. Os principais objetivos da análise RAM são aumentar a produtividade do sistema, aumentar o lucro total e reduzir o custo total do ciclo de vida dos ativos (que inclui custo de lucro cessante, custo de manutenção e custo operacional).
A figura 1 mostra as interações e aplicações da Engenharia de Manutenção com base na análise de RAM. Para um processo existente, os dados de manutenção devem ser registrados no sistema de manutenção para que possam ser analisados através de abordagens quantitativas e qualitativas.
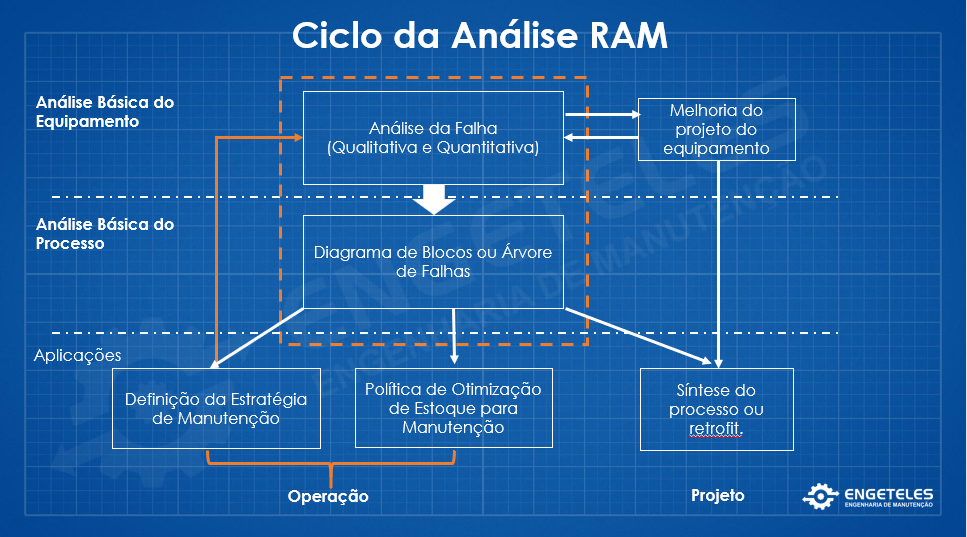
Através do FMEA – Análise dos Modos e Efeitos de Falha, serão mapeados os modos de falha e os parâmetros de distribuição e priorização serão obtidos para cada equipamento do processo.
Através dos Diagramas de Blocos de Confiabilidade (RBD) ou Árvores de Falhas (FT) é possível representar as relações lógicas entre falhas de componentes e falhas do processo, fornecendo a base para a Engenharia de Manutenção atuar através da análise RAM.
Com a distribuição de falhas entrada de dados em um RBD / FT, os engenheiros de manutenção serão capazes de entender a RAM, o desempenho atual do processo e prosseguir com os projetos para melhoria da confiabilidade, disponibilidade e mantenabilidade.
De fato, existe uma relação direta entre RBD e FT, mas a maioria dos engenheiros de manutenção e confiabilidade acham o RBD mais fácil de usar, já que ele pode ser mais facilmente relacionado a um fluxograma do processo.
Engenharia de Manutenção atuando na Confiabilidade (R)
Como dito, a confiabilidade é a probabilidade de um determinado item (equipamento, sistema, máquina, processo, etc.) desempenhar a sua função requerida de projeto durante um determinado período de tempo.
Existem várias formas da Engenharia de Manutenção garantir a Confiabilidade de um determinado item. Alguns exemplos:
FMEA – Análise dos Modos e Efeitos de Falha
FMEA é a sigla de Failure Modes and Effects Analisys, em português, Análise dos Modos e Efeitos de Falha.
O FMEA pode ser aplicado em projetos, produtos e processos. Tem o objetivo de identificar previamente as possíveis falhas que podem surgir, mapear como essas falhas se manifestam (modos de falhas) e quais seriam os efeitos dessas falhas caso aconteçam. Feito isso, essas falhas são hierarquizadas através do RPN, que é a multiplicação dos índices de ocorrência, severidade e detecção da falha.
O FMEA é a base para elaboração de um plano de manutenção centrada em confiabilidade. O Engenheiro de Manutenção deve participar ativamente da participação do plano de manutenção, principalmente colaborando para a construção do FMEA.
Hoje existem algumas ferramentas específicas para fazer o FMEA, porém, uma simples planilha no Excel conseguirá atender muito bem as necessidades. Uma vez que os princípios básicos e boas práticas para elaboração do FMEA foram levados em consideração.
Para a elaboração do FMEA, é função da Engenharia de Manutenção definir alguns termos comuns que serão usados:
- Falha: Perda de função ou performance do equipamento quando ela se faz necessária.
- Modo de Falha: A forma como a falha se apresenta no processo (sintoma).
- Efeito da falha: Impacto ou consequência que a falha traz ao processo.
- Ocorrência de falha: Quantas vezes isso já aconteceu ou tem probabilidade de acontecer.
- Severidade de falha: O quão grave e severa é a falha.
- Detecção de falha: Qual a possibilidade de encontrar essa falha antes que ela ocorra.
- RPN: Risk Priority Number – É o valor do risco calculado que fica associado ao modo de falha. Esse valor é a multiplicação dos níveis de ocorrência, severidade e detecção.
O primeiro passo para elaborar o FMEA pensando na elevação dos itens de confiabilidade é identificar os processos e seus equipamentos que serão analisados. O melhor método para tal é a análise de criticidade, uma ferramenta usada para avaliar como as falhas de equipamentos afetam o desempenho organizacional para classificar sistematicamente os ativos da planta para fins de priorização de trabalho, classificação de material, manutenção preventiva, manutenção preditiva e iniciativas de melhoria da confiabilidade.
Artigos Recomendados:
- FMEA – Análise dos Modos e Efeitos de Falha
- Planos de Manutenção: Como elaborar de forma eficiente?
- Curva PF: O que é e como usar?
Árvore de Falhas (FT) e Diagrama de Blocos de Confiabilidade (RBD)
No nível do processo, a Árvore de Eventos (ET), Árvore de Falhas (FT) e Diagrama de Blocos de Confiabilidade (RBD) podem ser usados para representar as relações lógicas entre modos de falha individuais do equipamento e modos de falha do processo.
Uma Árvore de Eventos usa ramificação binária para identificar os eventos que levam o processo a falhar ou ter sucesso. Em uma árvore de falhas, as falhas do processo podem ser expressas em termos de combinações de modos de falha de componentes.
Uma Árvore de Falha faz parte da Árvore de Eventos e pode ser elaborada a partir de uma Árvore de Eventos.
Um RBD (Diagrama de Blocos de Confiabilidade), conforme ilustrado na Figura 2 é um inverso lógico de uma árvore de falhas.Os blocos são usados ??para representar falhas de componentes ou modos de falha determinado componente.
A abordagem da análise de RAM adotada pelo processo explora os RBDs porque a maioria dos engenheiros de manutenção considera o RBD mais fácil de usar, pois pode ser mais facilmente relacionado a um fluxograma de processo. Com os parâmetros de distribuição inseridos em um RBD (ou ET ou FT) o desempenho do processo será obtido por simulações.
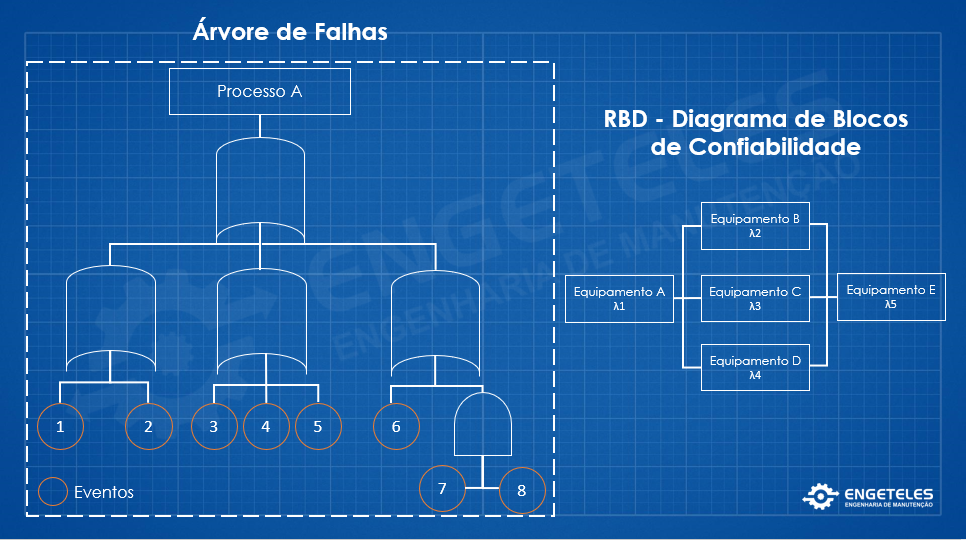
Artigos Recomendados:
Assista ao vídeo abaixo para ver a aplicação prática:
Engenharia de Manutenção atuando na Disponibilidade (A)
Ao contrário da Confiabilidade, a Disponibilidade é um cenário passado. Portanto, os indicadores usados para controle da disponibilidade são reativos.
Uma vez que a Engenharia de Manutenção consegue garantir a confiabilidade, é possível sentir os reflexos na disponibilidade. Sendo que ambas têm uma variável em comum: O MTBF.
O MTBF, que significa Tempo Médio Entre Falhas (sigla para Mean Time Between Failures), compõe o cálculo de disponibilidade e confiabilidade. Portanto, se a engenharia de manutenção atuar com foco na elevação do MTBF, ambos indicadores irão ter elevação.
A disponibilidade é uma métrica importante usada para avaliar o desempenho de equipamentos reparáveis, representando as propriedades de confiabilidade e manutenção de um componente ou sistema. No entanto, diferentes classificações de disponibilidade e diferentes maneiras de calcula-las.
A classificação de disponibilidade é algo flexível e é amplamente baseada nos tipos de tempo de inatividade utilizadas na indústria e na relação com o tempo (ou seja , o período de tempo a que se refere a disponibilidade). Como resultado, há uma série de classificações diferentes de disponibilidade, incluindo:
- Disponibilidade instantânea (ou ponto);
- Disponibilidade média de tempo de atividade (ou disponibilidade média);
- Disponibilidade constante do estado;
- Disponibilidade Inerente;
- Disponibilidade Operacional.
O foco da Engenharia de Manutenção deve ser elevar a Disponibilidade Inerente. A Disponibilidade inerente leva em consideração apenas os temos de indisponibilidade ocasionados por falhas funcionais.
Expressada através da fórmula:
Artigos Recomendados:
- Disponibilidade Inerente: O que é e como calcular.
- MTBF: Mean Time Between Failures – Tempo Médio Entre Falhas (Clique e saiba mais!)
- MTTR: Mean Time To Repair – Tempo Médio para Reparo (Clique e saiba mais!)
Assista ao vídeo abaixo e veja como calcular corretamente a disponibilidade dos equipamentos:
Engenharia de Manutenção atuando na Mantenabilidade (M)
A Manutenibilidade é a capacidade de um item ser mantido ou recolocado em condições de executar suas funções requeridas, sob condições de uso especificadas, quando a manutenção é executada sob condições determinadas e mediante procedimentos e meios prescritos.
Podemos resumir a mantenabilidade em: facilidade que uma equipe encontra em realizar atividades de manutenção.
Imagine que em uma determinada indústria metalúrgica, temos uma máquina de empacotar de engrenagens. Essa máquina é uma das
principais do processo de produção e se ela parar toda a linha de produção irá parar junto. Em um levantamento sobre as última falhas da máquina, chegou-se a conclusão que a máquina parou 32 vezes por problemas relacionados a “Superaquecimento do motor elétrico principal”.
Após uma criteriosa analise de falhas, foi identificado que a causa dessas falhas era a obstrução dos filtros das janelas de ventilação da cabine do motor elétrico.
Sabendo dessa anomalia, foi ordenado que fizesse a substituição desses filtros de forma semanal. E foi aí que começou o problema.
O local era de difícil acesso, essa atividade era nova e ninguém sabia a forma correta e mais ágil de se fazer, esse filtro era um modelo específico fabricado exclusivamente para aquele equipamento, não tinha no estoque da empresa e o seu processo de compra era demorado, além de tudo, essa atividade era em um espaço confinado e havia a necessidade de uma série de procedimentos para realiza-la de forma segura.
Enfim, se analisarmos o cenário acima, podemos dizer que a manutenibilidade da empacotadora de engrenagens para essa determinada ação de manutenção era muito baixa. Ou seja, essa atividade tinha um alto nível de dificuldade.
Pontos de elevação da Mantenabilidade por meio da Engenharia de Manutenção:
- Considerar a facilidade de acesso em que o técnico terá às conexões e pontos de inspeção;
- Verificar conjuntos que necessitam ser içados durante a manutenção e oferecer uma solução rápida e segura;
- Verificar o conforto ergonômico do técnico durante a execução;
- Revisar a zona de trabalho e otimizar os layout visando eliminar improdutividades;
- Revisar obstrução que um sistema causa sobre o outro (tubulações sobrepondo cabos, cabos sobrepondo proteções, etc.)
O trabalho na mantenabilidade do equipamento começa no momento de definir o seu projeto. É comum equipamentos antigos terem péssimos índices de mantenabilidade, pelo fato de que esse item começou a ter sua devida importância e atenção em meados dos anos de 1990.
Um dos principais reflexos que existe uma oportunidade de melhoria nos índices de mantenabilidade é o MTTR.
O MTTR (Mean Time To Repair) indica que o tempo para reparo dos equipamentos é alto, ou seja, a equipe está enfrentando dificuldades no momento da manutenção. Outro ponto que merece atenção é o Fator de Produtividade da mão de obra de manutenção.
É comum encontrar uma relação entre um alto índice de MTTR e a baixa produtividade da equipe.
Artigos Recomendados:
- Mantenabilidade: O que é e como ela pode te ajudar;
- MTTR- Mean Time To Repair;
- Fator de Produtividade da Mão de Obra